Industrie 4.0 – die Digitalisierung in der produzierenden Industrie
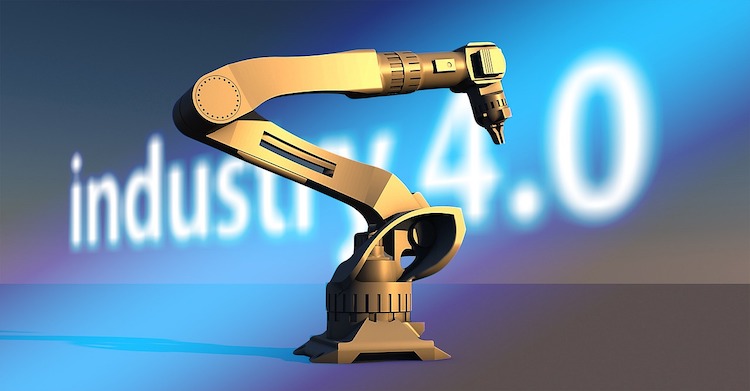
Seit einigen Jahren schon befindet sich die Fertigungsindustrie in einer Zeitenwende. Angekündigt wurde diese schon Anfang des letzten Jahrzehnts vom BmBF (Bundesministerium für Bildung und Forschung) mit dem Konzept der Industrie 4.0. Dabei soll unter Anwendung des Industrial Internet of Things (IIoT) die reale und die virtuelle Welt noch stärker zusammenwachsen.
Ziel des Vorhabens ist es, die Produktionsabläufe und Wertschöpfungsketten innerhalb der produzierenden Industrie Schritt für Schritt zu optimieren. Firmen, die dem Konzept offen gegenüberstehen, gelingt es zunehmend, die Produktivität zu steigern und die Kosten zu senken. Unternehmen, die sich den neuen Technologien verweigern, werden in absehbarer Zeit nur noch die Rücklichter ihrer Konkurrenten sehen.
Was wird unter dem Konzept Industrie 4.0 verstanden?
Zum ersten Mal zur Anwendung kam der Ausdruck “Industrie 4.0” im Jahre 2011 auf der Messe in Hannover. Diese gilt als weltweit wichtigste Drehscheibe hinsichtlich der industriellen Transformation.
Damit sollte verdeutlicht werden, dass Unternehmen zukünftig moderne Kommunikation- und Informationstechnologien nutzen müssen, um Umsatz und Gewinn zu steigern. Bei der so entstehenden Smart Factory kommunizieren intelligente Maschinen und Produktionsstraßen selbstständig untereinander und mit angeschlossenen Systemen. Das Herz eines solchen vernetzten Systems ist eine Plattform, wie sie unter anderem vom Marktführer thyssenkrupp in Form von toii als Digitalisierungslösung angeboten wird.
Zudem beschreibt der Begriff Industrie 4.0 die Dimensionen, die mit der Digitalisierung im Fertigungsprozess einhergehen. Wird darin doch nichts weniger als der vierte Schritt der industriellen Revolution gesehen.
- Industrie 1.0: Der erste Schritt der industriellen Umwälzung wird Mitte des 19. Jahrhunderts durch die Erfindung der Dampfmaschine ausgelöst.
- Industrie 2.0: Ende des 19. Jahrhunderts erreichte die industrielle Revolution mit der Einführung der Massenproduktion ihre zweite Stufe.
- Industrie 3.0: Die dritte Stufe wurde Ende der 1960er Jahre erklommen. Ausschlaggebend waren der Einzug von Automatisierung und Computertechnologien in die Fertigungsbetriebe.
- Industrie 4.0: Mit der Nutzung des IIoT gelingt es, nicht nur einzelne Betriebe zu optimieren, sondern die gesamte Wertschöpfungskette zu verbessern.
Was beinhaltet IIoT?
Grundlage von IIoT ist das Internet of Things (IoT). Diese Technologie findet Verwendung im Smart Home, in dem die unterschiedlichsten Geräte mit dem Ziel vernetzt werden, die Anforderungen der Bewohner hinsichtlich Sicherheit und Komfort zu erfüllen. IIoT gilt dabei als Unterdisziplin, ist aber bei weitem komplexer angelegt, werden doch ganze Branchen miteinander vernetzt.
Damit IIoT funktioniert, werden alle Maschinen mit sensiblen Sensoren ausgestattet. Diese ermöglichen einen stetigen Datenfluss, der es der Entscheidungsebene im Unternehmen erlaubt, Fehler im Produktionsprozess sofort zu erkennen und entsprechende Maßnahmen in Echtzeit zu ergreifen. Das Besondere dabei ist, dass sich IIoT nicht nur auf die einzelne Fabrikhalle beschränkt. Vielmehr findet die gesamte Wertschöpfungskette Berücksichtigung, indem Rohstoffproduzenten, Lieferanten, Kunden und das Recycling mit einbezogen werden.
Welche Anwendungen erlaubt IIoT?
IIoT gestaltet die Produktion branchenübergreifend effizienter. Daraus entstehen zahlreiche Wettbewerbsvorteile, die mit den nachfolgend angeführten Aspekten in Verbindung gebracht werden:
- Intelligente Justierung von Produktionsstraßen und Gebäuden.
- Umfangreiche Datenanalysen mithilfe von Big Data.
- Überwachung und Kontrolle aller Produktionsabläufe in Echtzeit.
- Optimierung der Lieferketten.
- Anpassung der Lagerbestände.
- Schonung der Ressourcen.
Warum ist eine möglichst rasche Umstellung auf Industrie 4.0 lohnend?
Schon heute profitiert die Fertigungsindustrie in hohem Maße von IIoT und der damit verbundenen Automatisierung:
- Fertigungsdaten in Echtzeit: Die Entscheider haben jederzeit und überall einen kompletten Überblick über den aktuellen Produktionsstand.
- Optimierung der Produktionsprozesse: Der umfassende und stetige Datenfluss lässt eine komplette Überwachung der Produktionsabläufe zu. Dieser erlaubt es den Verantwortlichen, Schritt für Schritt an der Feinabstimmung der Prozesse zu arbeiten und diese kontinuierlich zu verbessern.
- Anpassung der Lagerbestände und Lieferketten: Die Lieferung von Rohstoffen, Energie und sonstigen Komponenten des Produktionsprozesses lässt sich in Echtzeit verfolgen. Maßnahmen zur Anpassung können sofort vorgenommen werden.
- Qualitätssteigerung: Durch die Verknüpfung der Daten verschiedener Herkunft wird es möglich, stetig die Qualität der Produkte zu verbessern.
- Weniger Produktionsstopps: Die Sensoren an den Produktionsanlagen liefern stetig Daten über den Zustand der Maschinen. Fehler werden frühzeitig erkannt, indem die Maschinen eine Überschreitung von Grenzwerten vorab ankündigen. So lassen sich Wartungsarbeiten durchführen, bevor die gesamte Produktion stoppt.
Veröffentlicht von:
Letzte Veröffentlichungen:
Bauen, Wohnen und Garten24. April 2024Lichterketten: Magische Atmosphäre in Südwestfalens Gärten und auf Balkonen
Verschiedenes19. April 2024Urlaubsgrüße aus Südwestfalen: 10 Orte, die einen Ausflug wert sind
Verschiedenes18. April 2024Unbemerkt viel Geld sparen? Das sind unsere Ideen
Verschiedenes15. April 2024Anna Deimann und AD Consulting GmbH: Eine Erfolgsgeschichte im Zeichen des Unternehmertums